摘要:介绍了
粉末涂料的喷涂工艺流程、喷涂设备及烘干系统,对多颜色串色问题提出了解决方案,制定了汽车车厢用
粉末涂料的技术指标,并举例说明了验证粉末涂料与前处理电泳防腐配套性能的方法。
前言
目前,汽车车厢面漆喷涂多采用传统溶剂型油漆,需要增加废气收集治理设施,故存在投资巨大、运营费用较高、企业经营压力较大等问题。
粉末涂料具有无“三废”(废水、废渣、废气)排放的技术特点,同时其利用率高达95%,具有明显的环保优势,并可极大地降低涂装成本。
为满足环保法规要求,不增加生产成本,笔者所在公司组织开展了粉末涂料在汽车车厢上的应用研究。
1 粉末涂装工艺及装备
粉末喷涂工艺的原理与油漆静电喷涂基本相同。工件通过输送链进入喷粉房的适宜位置后,静电发生器通过喷枪枪口的电极针向工件方向的空间释放高压静电(负极),使从喷枪口喷出的粉末和压缩空气的混合物以及电极周围的空气电离(带负电荷)。
工件经过挂具通过输送链接地(接地极),这样就在喷枪和工件之间形成一个电场,粉末涂料在电场力和压缩空气压力的双重推动下到达工件表面,依靠静电吸引在工件表面形成一层均匀的涂层。
粉末涂料由固态树脂、颜填料、固化剂和助剂组成。粉末涂料静电附着后绝缘电阻都较高,能安定地附着在被涂物表面,在加热步骤中经加热熔融、流平,高分子之间发生化学交联固化而成膜。
成膜后的树脂具备优异的耐候性、耐化学性、热稳定性及机械性能。
1.1 工艺流程
1.1.1 素色粉末喷涂生产工艺流程
前处理→电泳→烘干→焊缝密封→粉末素色面漆喷涂→烘干(160~180°C,8~10min)→强冷→检查精修→下线。该工艺与油漆喷涂工艺相比工序不变,只将喷涂面漆改为喷粉。
1.1.2 两种金属粉末喷涂工艺路线
路线一:前处理→电泳→烘干→焊缝密封→金属粉末喷涂→烘干(160~180°C,8~10min)→强冷→粉末罩光喷涂→烘干(180~200°C,20min)→检查精修→下线。
路线二:前处理→电泳→烘干→焊缝密封→金属粉末喷涂→烘干(160~180°C,20min)→检查精修→下线。
路线一的优点是工艺成熟,质量风险小,但需要进行两次粉末喷涂,且在金属粉末喷涂完成后需要进行一个高温短时间的烘干过程,导致生产线过长,生产能耗较高;
路线二与素色粉末工艺的路线相同,更简洁,但缺点是对金属粉末涂料的要求较高,需要一次成膜就能得到所需要的外观质量,施工要求也较高。
1.3 粉末涂料的工艺设备及串色解决方案
1.3.1 喷涂设备
粉末喷涂设备主要由粉房、供粉系统、大旋风回收系统、喷枪等组成,如图1所示。
粉末喷涂之所以比较经济,主要原因是其理论利用率高达95%,但实际利用率还与方案设计、人员操作、生产组织等密切相关。
单从设备角度分析,粉末利用率与大旋风分离效率、回收粉使用率这两个指标有关。
大旋风的作用是使得粉末颗粒与风分离,粉末颗粒落入回收盒后由回收粉泵送回供粉桶进行重新利用,其分离效果与内壁结构、风管角度设计、风机风量等有关(即由设备的基本特性决定,效率最大能达到97%)。
1.3.2 热辐射烘干系统
粉末涂膜的烘干条件为:160 ~ 180°C,20min。烘干系统可以采用热风循环和红外辐射两种方式。
本项目的生产线在切换为粉末喷涂之前采用热风循环烘干系统(要求140°C),切换后考虑到烘干温度提升对能源的损耗以及粉末涂料熔融阶段所需温度较高,因此在现有生产线基础上引进催化红外加热技术,见图2。
在升温一区采用红外辐射加热,确保粉末涂料快速熔融,升温二区和保温区保留热风循环烘干系统,确保粉末涂料完全固化。
与传统热风循环烘干系统相比,催化红外加热技术通过燃气在加热板表面产生氧化反应,将多数的热以中波红外线的形式辐射出去;
专门加热涂料中的羧基与烃基分子,故只对涂料加热,对板材无明显加热效果,加热过程无需点火,完全无焰,绝对防爆。
1.3.3 多种颜色喷粉的串色问题
由于同一个粉房生产多种颜色,在大旋风内部一般会残留杂色粉末,当杂色粉末混入新粉末而进入回收系统后,就会产生串色质量问题。
为避免此问题,一般换色后需要空喷5~10min,以便将设备内部残留的杂色粉末带出,然后才进行工件喷涂。
由于空喷的粉末不再被利用,因此该方法虽然可以避免串色,但造成大量的粉末浪费,降低了粉末利用率和经济性。
为保证粉末利用率,并避免串色等质量问题,设计了干碰干的喷涂工艺:第一遍喷涂回收粉,第二遍喷涂新粉,两遍喷涂在同一个粉房进行,两遍之间不烘干,实际仍是一遍成膜。
如图3所示,自动喷枪组1和2喷涂回收粉末,自动喷枪组3和4喷涂新粉。回收粉内混入的杂色会被新粉覆盖,漆膜表面仍为全新粉末,质量不受影响,此方案可实现回收粉末的100%利用。
针对的汽车车厢生产线为重型、轻型商用车匹配车厢,采用“硅烷前处理+底面合一阴极电泳+粉末喷涂”的工艺,颜色繁杂,多达30种以上。对该生产线2年内排产的颜色进行梳理,明确开发9种颜色的粉末涂料,它们在2年内的总排产量中占比达95%以上。
量产主色有汉玉白、尊贵蓝和炫丽红,特殊颜色有炫酷黑、工程黄、旺旺红、水晶紫、蜜橙和邮政绿,另外确保剩余小颜色产量的VOCs(挥发性有机物)排放满足国家规定的限值要求。涂料开发验证采用生产线同一型号试板,并随线进行前处理电泳制板,后统一在粉末开发实验室进行喷粉及性能检测,粉末试板涂膜外观技术指标均满足开发前制定的技术指标,并完成外观数据检测评审确认。以炫丽红为例,粉末试板涂膜外观及其技术指标达成情况见表1。
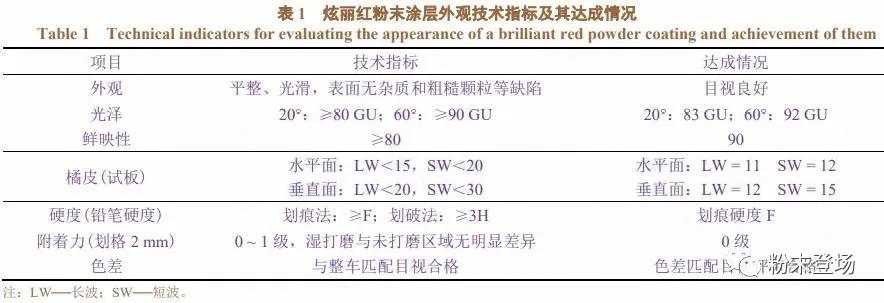
2.2 粉末涂料配套性研究
涂装线前处理采用锆盐−硅烷复合型无磷转化工艺(即硅烷前处理工艺),具有不含重金属的环保特性,在冷轧钢板、热轧钢板等板材表面均能形成良好的转化膜,与阴极电泳漆配套性良好,电泳质量损失小,生产过程中渣的生成量低。
所用的黑色双组分底面合一阴极电泳漆能够与前处理和粉末面漆形成优良的配套。
为验证粉末涂料与前处理电泳漆的配套性,考察了相应配套后的耐盐雾和耐湿热性能,相关技术指标与测试方法见表2。
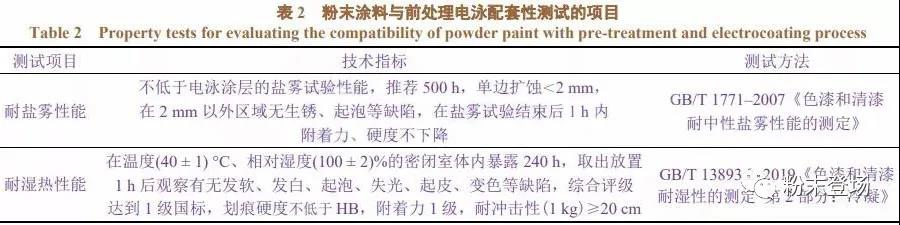
采用A、B两种硅烷前处理材料分别与底面合一阴极电泳漆和纯环氧阴极电泳漆交叉制板,配套粉末涂料后的性能测试结果见表3。
由未
喷涂粉末的前处理电泳板盐雾扩蚀的结果可知,底面合一电泳漆对硅烷前处理具有选择性,不同型号硅烷前处理搭配底面合一电泳时的表现不同。
而不同类型硅烷前处理与纯环氧电泳漆的搭配都具有良好的防腐性能。
喷涂粉末后,在前处理电泳底漆的防腐前提下,涂膜的防腐性能均有提升,且耐盐雾和耐湿热测试后的附着力、硬度、耐冲击等机械性能均满足技术指标要求。
2.3 粉末涂料外观及涂膜性能验证
为确定粉末涂层的颜色、外观、耐候性、耐化学品性、耐老化等性能是否达到了汽车涂装产品的质量要求,开展了相关性能验证试验,对氙灯老化、耐水、耐湿热、耐温变、大气曝晒等重点性能也进行了详细验证。
经检查,所有项目均满足产品品质要求。以炫丽红为例,各项测试的技术要求及检测结果见表 4,其中大气曝晒持续时间较长,仍在检测中。
粉末工艺是国家推荐使用的环保经济型新工艺,已初步在汽车工业生产上应用。为进一步扩大其应用范围,满足生产线环保排放的要求,需要加强对粉末涂料的应用研究。开发更多色彩的粉末涂料,并尽快在汽车上应用,以降低企业经营的法律风险和效益压力,进一步提升产品竞争力,从而走上轻量化绿色节能之路。